Testing
Avantium Flowrence XR
The Flowrence XR is a high-throughput nano-flow fixed bed unit allowing the evaluation of solid catalyst's performances under various conditions (CO2/CO hydrogenation, Fischer-Tropsch process, Hydroprocessing). The unit can be adapted to specific reaction conditions upon request.
The main features of the Flowrence XR are:
- 16 fixed-bed reactors spread equally in four temperature blocks.
- Each reactor contains typically 10 to 500 mg of catalyst.5 different gases and 1 liquid feed can be combined
- Up to 80 bars at max 500 °C
- Temperature controlled automated liquid sampler
- Fully automated with two online gas chromatographs detecting permanent gases and up to C16 hydrocarbons in the gas phase allowing 24/7 extremely accurate data recording.
HEL CAT96
The CAT96 is an automated batch catalyst screening unit that uses a standard MTP of glass vials as reactors. The unit aims at evaluating the catalytic performances of materials under CO/CO2 hydrogenation, hydroformylation, liquid hydrogenation... Other reactions can be adapted upon request.
The main features of the CAT96 are:
- Up to 250 °C and 100 bar
- Automated gas purge, data logging, multi-step recipes, parameter control and feedback loops.
- Can accept standard MTP with vials of various sizes 96*1 ml, 48*2 ml, or 24 *4 ml.
- Magnetic stirring for each reaction vial.
ILS 96x Batch Reactor Unit
The ILS has 96*20ml individual batch reactors to evaluate the performances of conventaional and air-sensitive catalyts for hydrogenation, hydroformylation and other gas/liquid reactions. It is dividied into 2 blocks of 48 reactors, each block having independant temperature and pressure control (up to180C and 100bars). The vials can be prepared with a seperated robotic unit, combining solid catalysts and liquid reactants / solvents and barcode tracking.
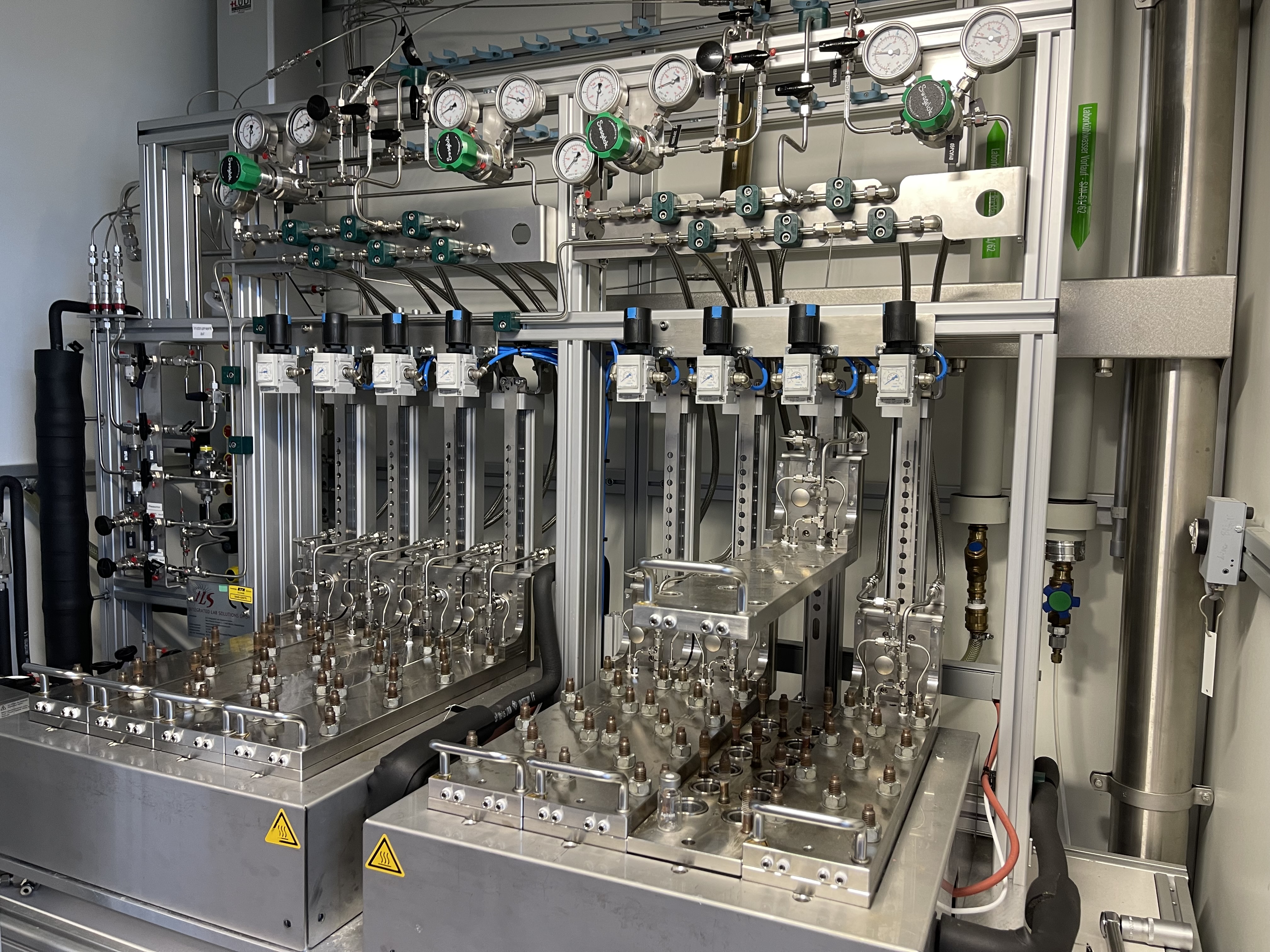
The key features of the ILS are:
- Vessel count: 96 (2 × 48)
- Maximum pressure: 80 bar
- Maximum temperature: 80 °C
- Stirring: Magnetic
- Control: Manual operation
- Compatible gases:
- N₂ (10 and 80 bar)
- H₂ (80 bar)
- Optional: CH₄, CO, CO₂, C₂H₄ (80 bar)
Chemspeed SwingXL Autoplant – Batch Reactor Screening Unit
The Chemspeed SwingXL Autoplant is a fully automated platform for high-throughput batch reaction screening, offering flexible, precise, and parallelizable control of chemical processes under pressure. It integrates both MTP pressure reactors and process development (PD) reactors, allowing for systematic exploration of a wide range of reaction conditions.
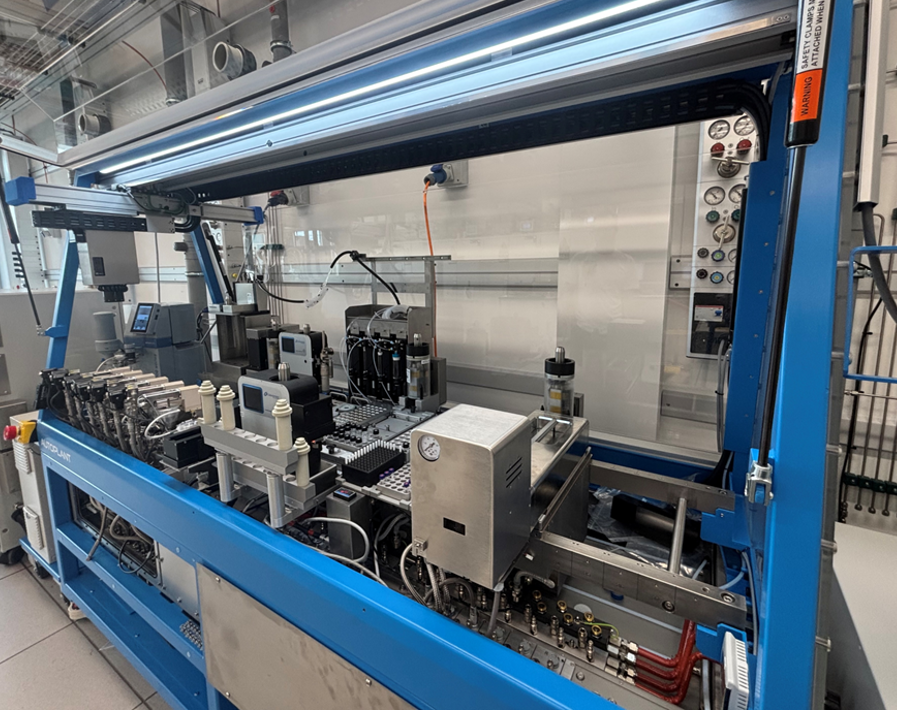
The key features of the Chemspeed SwingXL Autoplant are:
MTP Pressure Reactor Block
- Accommodates various multi-well plate formats
- Individual temperature control: from –20 °C to 150 °C
- Agitation control: up to 600 rpm
- Enables high-throughput batch reaction screening in micro- to meso-scale volumes.
Process Development (PD) Reactors
- Six individually controlled high-pressure batch reactors
- Equipped with a supply module featuring high-pressure pumps for automated dispensing and aspiration of reagents and samples under pressure (up to 80 bar)
Gas Supply Integration
- Five gas lines connected to both MTP and PD reactors for screening reactions under different atmospheres (H₂, CO₂/H₂, CO/H₂, and other custom gas mixtures)
Unchained Labs Big Kahuna (in Glovebox) – Air-Sensitive Catalyst Testing Platform
The Unchained Labs Big Kahuna, housed inside an MBraun glovebox, is a fully automated robotic platform engineered for air-sensitive catalyst synthesis and batch testing. This configuration is tailored for inert atmosphere workflows, supporting high-throughput screening and precise control of reaction conditions. A built-in carousel module provides scalable storage and handling of catalysts and reaction plates, enhancing operational efficiency.
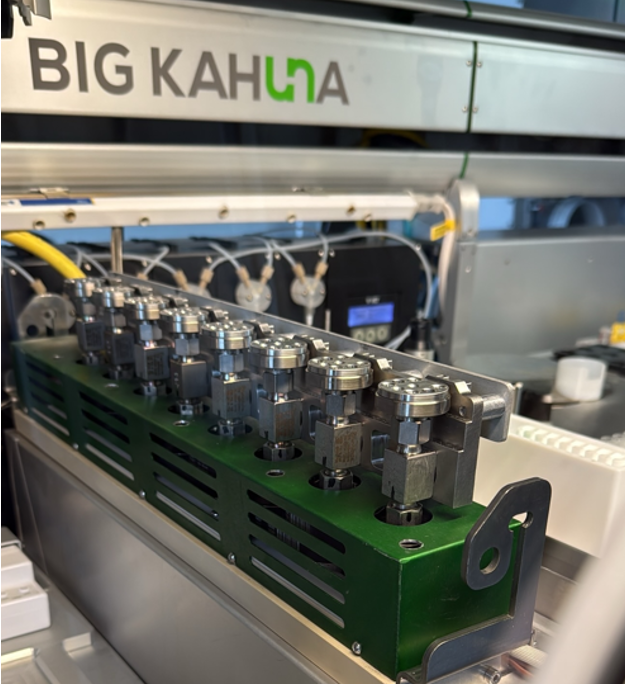
The key features of the BK Catalyst Testing Platform are:
Precise Control of Reaction Conditions
- Pressure control: up to 50 bar
- Temperature control: up to 250 °C
- Stirring speed: up to 1000 rpm
Pressurized Operation & Sampling
- Accurate injection of reagents under pressure
- Safe and reproducible sampling during reactions
Additional Automation Capabilities
- Automated solid and liquid dispensing into vials: 2, 4, 8, 20, and 125 mL
- Thermal control and agitation for up to 9 multi-well plate formats (MTPs)
- Integrated filtration module for automated GC/HPLC sample preparation
- Barcode tracking for full digital traceability of catalysts, vials, and reaction conditions